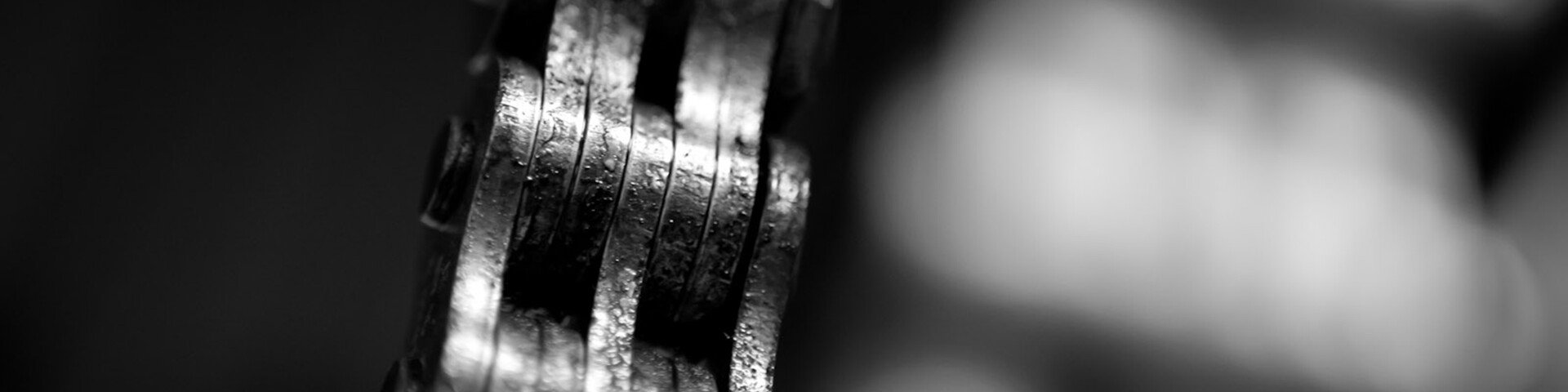
- Home
- News
More possibility to control your hookloader from external devices
PALFINGER’s hookloaders can already be controlled from an external device, like a crane, thanks to the PAD controller interface. This enables the adjustment of the equipment position with all the safety logic included, without leaving the main activity to return to the cabin to handle the arm. The interface is now featuring new functions for a better and more efficient integration and use.
Easier integration to save time and money
The solution is now protected in a waterproof housing ready for plug-in. The bodybuilder doesn’t have to find a homemade solution anymore to protect it. Mounting and development time is saved, as well as money.
To limit the number of switches needed to control the hookloader, 2 automatic sequences are now available. Each complete cinematic of tipping or sliding back/forward, including safety procedures, is operated with his dedicated switch. The integration on an external device is easier as it requires less switch and less mounting time. Both sequences are more efficiently added onto an existing controller.
Efficient use
The configuration of the box and the new interface programming allow both the radio control of the hookloader and a secondary external control for maximum flexibility for the user.
Epsilon now offers a dedicated fixed control for the hookloader in the top seat which provides versatility and convenience for operators. They no longer need to carry the radio control with them on the seat and can use the dedicated remote control to save space on the top seat while still accessing useful hookloader functions.
The PAD controller interface is particularly welcome in a crane – hookloader combination. Operators are always looking for more comfort and ease in the daily movements of their crane to be as efficient as possible. Thanks to the interface, they can move the container to the exact position that will require the easiest movement, the shorter cinematic to fill or empty the container with the grapples. The 2 main movements needed has been identified as:
-moving the container backwards / forwards on the truck to help to adjust the distance between the grapples and its content
- tipping the container up and down for example to gather its content.
Both movements are now available in automatic sequence to avoid any other manipulation of switches.
What will your application be?
There are other situations where it may be useful to move the container to facilitate the job of the workers, without wasting time to go back in the cab to move the arm. For example:
- asphalt application: Tipping operation can be done remotely for a more convenient and safer control, for people standing at the back of the equipment.
- robotic lifting equipment for refuse container: The sliding arm is actuated by the external control system according to the sequence required by the robotic lifting arm
What will your application look like?
For more information, do not hesitate to contact your local dealer.
ABOUT PALFINGER AG
PALFINGER is an international technology and mechanical engineering company and the world’s leading producer and provider of innovative crane and lifting solutions. With around 12,350 employees (without contract workers), 30 manufacturing sites and a worldwide, comprehensive sales and service network, PALFINGER creates added value from the challenges of its customers. PALFINGER is consistently continuing on its course as a provider of innovative, complete solutions that deliver increased efficiency and better operability, while leveraging the potential of digitalization along the entire production and value chain.
PALFINGER AG has been listed on the Vienna stock exchange since 1999, and in 2024 achieved revenue of EUR 2.36 billion.
For further information please get in contact with us: emea-marketing@palfinger.com