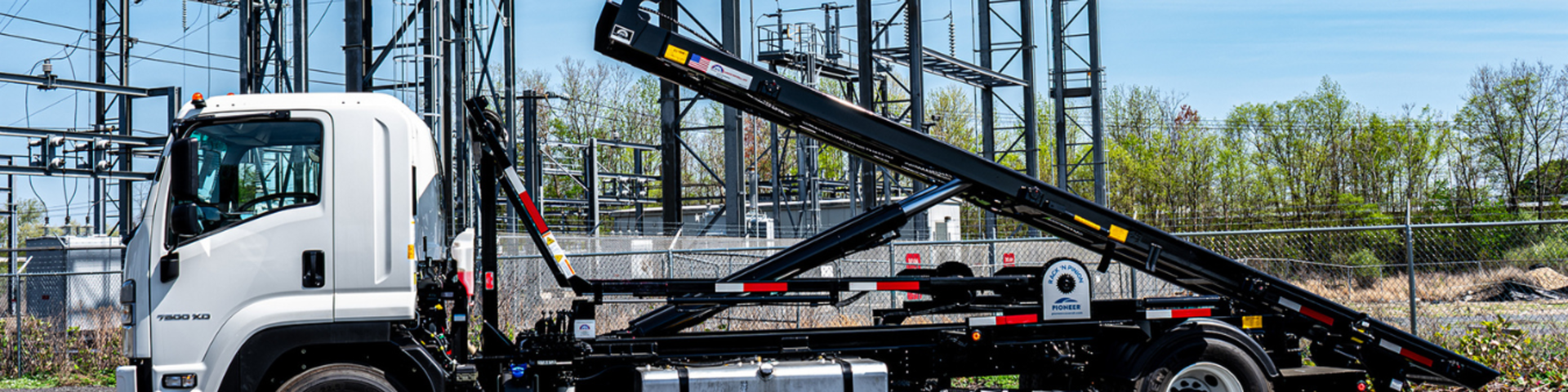
- Home
- News
Mantén en Óptimo Estado tus Carretillas Elevadoras Montables con estos 3 Sencillos Consejos de Mantenimiento
Roll-offs are essential for transporting heavy materials across various industries, from construction to municipal waste management.
Roll-offs are the backbone of waste management and recycling operations, used extensively for transporting large volumes of waste, scrap metal, and other heavy materials. Their versatility makes them essential in various industries—from construction to municipal waste management. However, despite their rugged design and heavy-duty capabilities, roll-offs are not immune to wear and tear. As a Roll-Off Service Manager with almost two decades of experience in the trucking industry, I have seen it all when it comes to roll-off equipment.
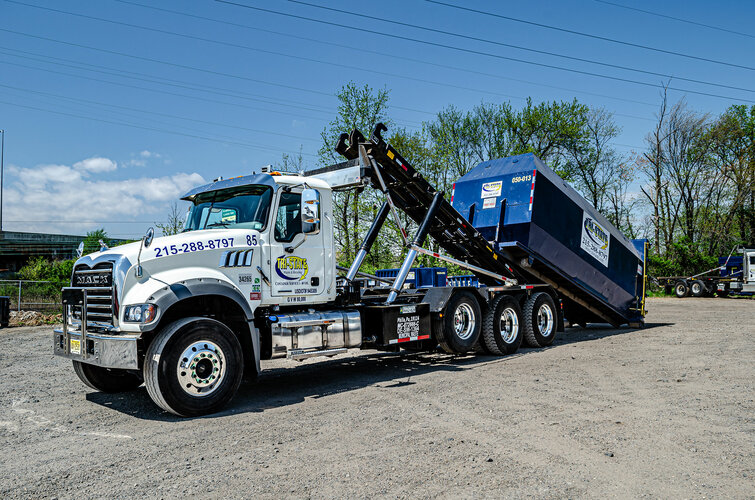
Roll-offs are the backbone of waste management and recycling operations, used extensively for transporting large volumes of waste, scrap metal, and other heavy materials. Their versatility makes them essential in various industries—from construction to municipal waste management. However, despite their rugged design and heavy-duty capabilities, roll-offs are not immune to wear and tear. As a Roll-Off Service Manager with almost two decades of experience in the trucking industry, I have seen it all when it comes to roll-off equipment.
Top Issues
While technology has certainly advanced over the years, the issues we encounter in the shop often remain the same. If left unchecked, these problems can lead to costly repairs and unexpected downtime, disrupting operations. The good news is that many of these problems are preventable with regular maintenance and a keen eye for detail. Here are the three most common roll-off issues that we see and how you can avoid them:
-
Frozen or Rusty Sheave Blocks and Side Rollers: One of the most common issues we encounter is frozen or rusty sheave blocks and side rollers. These components are crucial for the smooth operation of your roll-off hoist, but they are often overlooked until it is too late. When these parts seize up, it can cause significant downtime and costly repairs.
-
Premature Pump and PTO Burnout: Another frequent issue is the premature burnout of pumps and PTOs (Power Take-Offs). This can result in unexpected downtime and the need for early replacement, which is both time-consuming and expensive.
-
Cable Breakage: Cable breakage is another issue that can put a truck out of service until the cable is replaced. This not only leads to costly repairs but also affects productivity.
Prevention Tips for Avoiding These Common Issues
Whether you’re managing a fleet or handling a single unit, you can prevent these common issues by following these prevention tips. These practical steps will help you avoid frequent roll-off failures, reduce downtime, and ensure that your equipment remains reliable and safe in the long run.
Proper Hoist Selection
It is crucial to select the right hoist for your application. Be mindful of your hoist capacity—whether heavy-duty or standard—and ensure it matches your operational needs. Different hoists are designed for different functions, so choosing the correct one can prevent overloading and subsequent pump or PTO failure.
Chassis Rev Limiter
Ensure your chassis is equipped with a rev limiter, which stops the RPMs at a safe range, resulting in longer pump and PTO life. This small addition can make a big difference in preventing burnout.
Regular Lubrication
Lubricate your hoist at least once per week or every 40 hours of operation. Proper lubrication is essential for all types of bearings, gearing, and friction-producing mechanical devices. Without adequate lubrication, components can wear out prematurely due to increased abrasion or excessive heat.
Accessible Grease Points
Ensure you are hitting all the grease points, which are typically accessible on top of the shoe, pin, and side rollers. This simple step can extend the life of your components and keep your equipment running smoothly.
Regular Inspections
Examine your hoist cable, cable ends, clamps, and pins regularly. Look for signs of breakage, unraveling, or flat spots. Ensure that clamps are tight and not worn out.
Avoiding Shock Loads
Ensure that the equipment is used properly. For instance, when unloading a container, be cautious of slack in the cable. Allowing slack can result in a "shock load," which can cause the cable to break.
Hold Down Locks
Regularly inspect hold down locks for any excessive wear and ensure the container is fully secured at the rear.
Cylinder Inspections
Check your cylinders for any signs of wear or damage, and make sure they are functioning correctly.
Oil Levels
Always check the oil levels in your equipment to avoid running components dry, which can cause severe damage.
Driver Accountability
Driver accountability plays a crucial role in preventing these common roll-off issues. Drivers are the first line of defense against equipment failure. By performing daily and weekly inspections, they can identify potential problems before they escalate into costly repairs or safety hazards. Proper usage of equipment is equally important.
Daily Walkaround Checklist
To support driver accountability, implementing a daily walkaround checklist can make a significant difference in maintaining the health of roll-off equipment. This checklist should include:
-
Ensuring that backup and body-up alarms are functioning properly. Check all electrical connections and perform a functional test by engaging the reverse gear and raising the body. If any issues are found, replace the alarms immediately to maintain safety.
-
Checking all lights and replacing any that are out. Visually inspect all lights, including headlights, taillights, brake lights, and turn signals, for any signs of damage or burnt-out bulbs. Test each light to ensure it is working correctly and replace any faulty bulbs immediately. Clean the lenses to ensure maximum visibility and check electrical connections to prevent flickering issues.
In my years of experience, I have learned that the key to avoiding these common roll-off issues is consistent, proactive maintenance and strong driver accountability. By following the steps outlined above, you can keep your equipment in top shape, reduce downtime, and extend the life of your components. Remember, the time you invest in maintenance today can save you significant time and money down the road.
Acerca de Bobby Campbell
Bobby Campbell es parte de PALFINGER North America desde hace más de 6 años y actualmente es Gerente de Servicios de carretillas elevadoras montables. Veterano de la Marina con siete años de servicio en roles activos y de reserva activa, Bobby cuenta con casi 30 años de experiencia técnica que abarca un amplio espectro de maquinaria, incluyendo aeronaves, grúas, montacargas y vehículos.