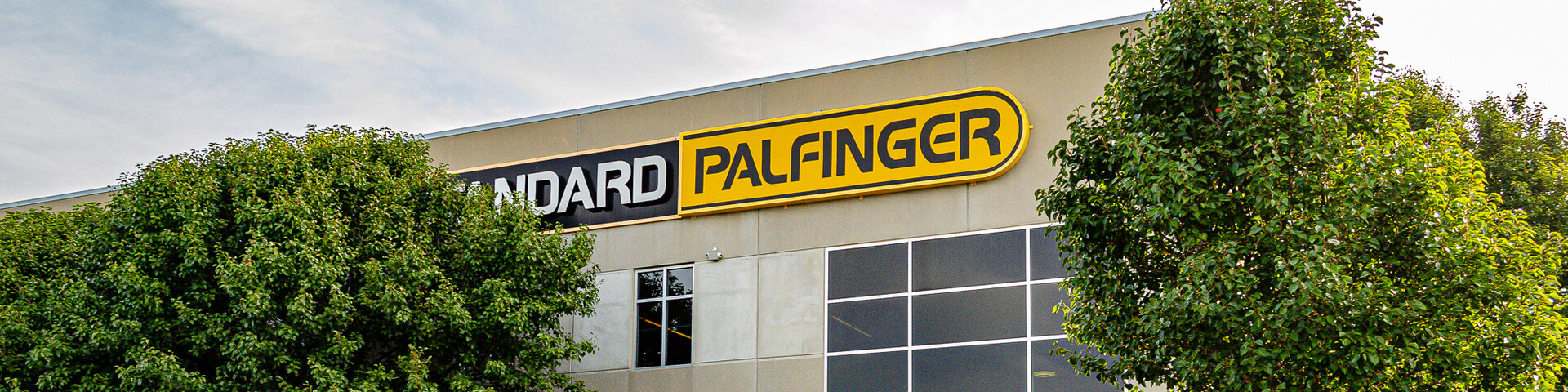
- Home
- News
Join Us for a Walk in Our Steel-Toed Shoes: Part 4
Over the past few months, we have taken you on the first part of our tour of PALFINGER North America, and we hope you have been enjoying the journey. The FOURTH stop is thriving Council Bluffs, Iowa, where our mechanics truck line was born. The skilled Engineering team you will meet works daily to design the service cranes and crane bodies we know and rely on. We are excited to introduce you to all of the very talented individuals in Council Bluffs!
Read Part 1 on the great team in Trenton, NJ.
Read Part 2 on the hardworking team in Oklahoma City, OK.
Read Part 3 on the fun team in Tiffin, OH.
In 2007, David Kovamees was looking for a reliable full-time job and interviewed for a welding position, but 16 years later, he came to find a lasting and fulfilling career. Throughout the years, he has been in many positions, from welding, and quality specialist, to the service department in warranty and technical support and spare parts. Each role he has held has helped build an excellent base as he grows into each new position.
As each day brings new challenges, David never has a dull moment, and with the support of his great team, there is no issue they can’t tackle. The accomplishments and the constant development of the Service Department are one of the things that David is the proudest of and said, “We still have a ways to go, but the improvement is noticeable in many aspects. Team development and processes continue to grow in each section of the department.” This does not end with his department, which is evident in many areas of PALFINGER. He also mentioned, “PALFINGER does not settle for ‘good enough’ and keeps pushing to lead the market. Other companies that are in similar fields seem to stall out and not advance, not here. There is a lot of investment and plans for the future.” He was recently promoted to Regional Spare Parts Manager and looks forward to what the future holds in this new role.
Fast forward to 2023, and David has this advice for new employees, “Get your foot in the door and never stop. This is a company that gives lots of room to grow and move up.”
When Michael Kanter walked into an interview for a Production Supervisor role, he had no idea that that interview would change his career. Midway through the interview, he was asked whether he would prefer Production or Quality, which quickly turned into an interview for a Quality Manager role. Over the years, he has been challenged with shifting the culture from reactive to proactive, which is no small feat. However, with the support of senior leadership, they were able to find the right people with the right skill sets to overcome their challenges. Now nearly eight years later, he is still as passionate about his role as he was on day one and mentioned, “It is nearly impossible for me to become bored, especially in a Quality role. Each day brings unique challenges that force us to see processes from different perspectives. I also deeply enjoy the relationships I’ve built with peer[s], with customers, with suppliers, and with other outside vendors.”
When asked about his favorite memories at PALFINGER, Michael couldn’t pick just one and said, “All my favorite moments are seeing others grow, personally and professionally. A welder who became a Team Lead and then a Supervisor. A coworker who will soon complete her graduate degree. One of my own team members who will soon complete his second graduate degree. Another welder who studied to become a Certified Weld Inspector/Certified Weld Educator. I love seeing people make [a] deliberate effort to gain new skills and advance their careers.”
Michael’s advice to new employees: “You must understand that PALFINGER is a dynamic environment, always evolving. A global entity which grows by acquiring local businesses that manufacture complementary product portfolios must eventually fully integrate those local units into the larger organization. This path is rarely straight or even obvious, especially in the early stages of the process. Mental flexibility and a commitment to personal growth are key attributes for a successful contributor!”
Trivia: Michael has an undergraduate minor in Biblical languages and can read koine Greek. He has also studied German, Latin, Greek, Hebrew, Spanish, Italian, and the entire history of English, starting from its early days as a Germanic dialect.
Khullyee Moyer is no stranger to manufacturing as it is the industry her whole family has been in. Two years ago, she started as an assembler and quickly fell in love with working with her hands. Shortly after starting, she was offered the lead position in her department. She provides her team leadership and guidance daily to ensure that her department runs smoothly and efficiently. Over the years, her drive has continued to grow. She mentioned, “I travel a few times a year, and since starting with PALFINGER, I am constantly looking at the back of trucks and trailers for our product. When I do see a liftgate so far from home, it really puts things into perspective of just how large our company is. I recently visited a car show in McClelland, Iowa, and saw an older PALFINGER body. I took pictures of this truck because I was so excited to see something that came from my line of work. Far away or close to home, it thrills me to see our product and know the hard work, dedication and manpower it takes to make each product. “
One of the proudest moments in Khullyee’s tenure was when she finally perfected plasma cutting. “Through high school, you are asked what you would like to do after graduation. I knew I wanted to jump right into finding what my passion was, so I worked many jobs trying to figure it out. When I found PALFINGER, I knew I wanted to work with my hands [for] the rest of my life and staying active is a priority of mine, so this job brought both of those things together,” she said.
Khullyee’s advice to new employees: “Never stop asking questions. I understand how intimidating a field of this nature may be, but it is so important to ask questions without fear of being judged or ridiculed. It takes time to really understand a work environment, and asking questions will help a lot. Spend some time alongside of other employees and develop a work relationship with someone you look up to as a PALFINGER employee.”
Trivia: She rides a 2008 Honda CBR 600rr, and it is one of her primary stress relievers!
Almost two years ago, Clifford D. Ottensen, Jr. started with PALFINGER as a liftgate assembler. While he is very passionate about working with his hands, one of his proudest moments was learning to build a liftgate from his coworker, Dustin, who is hearing impaired. The pair work well as a team, and with Dustin’s guidance, insight and teaching, Clifford has excelled in assembly.
One thing that fascinates Clifford the most is PALFINGER’s growth, and he mentioned, “I’m proud to be a part of a company that’s striving to be the best at what we do as a company.” Each day he comes in, he looks forward to where not only will he grow but where the company will also grow.
Clifford’s Advice to New Employees: “Be aware of your surroundings and avoid pinch points. Show up ready to work and be on time.”
Trivia: He is almost 50 years old and has five grandchildren.
Robert Engdahl has been promoted to Regional R&D Sr. Director NAM. At the time of submission, he was head of the Engineering team in Council Bluffs.
Where has the department made the most impact?
"The department has developed and sustained a high-quality product design that supports the company's vision to provide industry-leading solutions to our customers,” mentioned Robert Engdahl. Some of their members were fortunate enough to spend almost three months working with the SBC team in Austria, which is helping to design our new products. They were able to teach the Austrian team about the products, customers, and market. Collaborating and learning from each other has definitely helped our team design better products. Not only are they working on developing new products, but also improving current processes. Continuous improvement is an area they keep a close eye on, and have worked to implement engineer change notifications (ECNs) to help production efficiency.
What is your team most proud of?
Learning and adapting are vital to the engineering team. They are not afraid of making mistakes as it can be a great learning experience that helps them to adapt and not replicate the mistake. Working in new product development enables them to see the full picture of the product lifecycle as they are able to create designs that make positive impacts on the product and the customers. They are constantly working on improving our products and bringing the best solutions to our customers.
What is your favorite thing about your industry and the products you work with?
“PALFINGER customers are open to adopting new technology that provides an advantage in their day-to-day work, and an industry that is open to advancement allows engineers to be ambitious in product design,” said Robert. The Engineering team having the chance to see their designs come to fruition and get implemented into production is something that not everyone gets a chance to see. “Watching things grow from a single flat sheet metal piece and when it leaves the building, it is a fully painted body and crane,” mentioned Steven Walker.
If you could describe the team in one word, what would it be?
Enterprising, Efficient, Collaborative, Cohesive, and Amazing!
Know Your Engineers
Match the engineer with the correct fact. The first person to submit the correct matches will receive a PALFINGER vest and PALFINGER tumbler! Will update once we have determined a winner. Council Bluffs Engineering Team is excluded from this contest.
What is something that other employees may not know about you?
Engineer:
Steven Walker
Colten Ransdell
Rob Engdahl
Tyler Villbrandt
Facts:
• Earned a brown belt in Karate when in elementary school
• Certified scuba diver and dream is to go scuba diving with sharks
• Learning to speak German
• Is an Avid Bowler
Submit Answers
Council Bluffs: Reliability You Can Count On
The Omaha Body Company produced many goods from the 1920s until the 1960s, including spark plugs, airplane parts, center dump gravel trailers, etc. All manufacturing was concentrated in a cutting-edge 210,000-square-foot facility in 2006 with an onsite e-coat system. On October 31, 2008, PALFINGER AG purchased Omaha Standard. After being acquired by PALFINGER AG, they launched a full line of mechanical service bodies, telescopic cranes, and hydraulically powered air compressors.